Porosity in Welding: Identifying Common Issues and Implementing Ideal Practices for Prevention
Porosity in welding is a prevalent concern that often goes undetected till it triggers significant troubles with the honesty of welds. This typical problem can compromise the toughness and durability of bonded frameworks, positioning safety threats and causing expensive rework. By understanding the origin triggers of porosity and implementing reliable avoidance strategies, welders can significantly boost the high quality and reliability of their welds. In this conversation, we will discover the essential factors adding to porosity formation, analyze its harmful effects on weld performance, and go over the most effective techniques that can be embraced to decrease porosity incident in welding procedures.
Usual Causes of Porosity
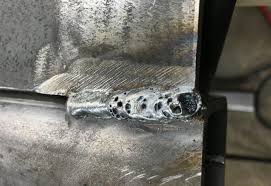
Utilizing filthy or wet filler products can introduce impurities right into the weld, contributing to porosity issues. To mitigate these usual reasons of porosity, extensive cleaning of base steels, appropriate shielding gas option, and adherence to ideal welding parameters are crucial methods in achieving high-grade, porosity-free welds.
Effect of Porosity on Weld Quality

The presence of porosity in welding can considerably endanger the structural stability and mechanical residential or commercial properties of bonded joints. Porosity develops voids within the weld steel, deteriorating its total strength and load-bearing capability.
Among the key consequences of porosity is a reduction in the weld's ductility and sturdiness. Welds with high porosity degrees tend to display lower influence toughness and decreased capacity to warp plastically prior to fracturing. This can be specifically concerning in applications where the welded elements undergo vibrant or cyclic loading problems. Porosity can restrain the weld's capacity to properly send pressures, leading to early weld failing and possible safety and security threats in essential frameworks. What is Porosity.
Ideal Practices for Porosity Avoidance
To boost the structural stability and top quality of bonded joints, what particular procedures can be implemented to reduce the incident of porosity throughout the welding procedure? Utilizing the correct welding technique for the details material being bonded, such as adjusting the welding angle and gun position, can additionally stop porosity. Normal examination of welds and immediate removal of any kind of issues determined throughout the welding process are crucial practices to protect against porosity and generate top notch welds.
Value of Proper Welding Methods
Executing appropriate welding methods is extremely important in ensuring the structural integrity and quality of bonded joints, building upon the structure of reliable porosity avoidance actions. Welding techniques directly influence the total toughness and durability of the bonded framework. One crucial element of appropriate welding techniques is maintaining the correct warmth input. Too much warm can result in enhanced porosity due to the entrapment of gases in the weld swimming pool. Alternatively, not enough warm may cause insufficient combination, creating possible weak factors in the joint. Furthermore, utilizing the suitable welding parameters, such as voltage, existing, and take a trip speed, is crucial for attaining sound welds with minimal porosity.
Moreover, the choice of welding process, whether it be MIG, TIG, or stick welding, need to line up with the details requirements of the task to ensure ideal results. Appropriate cleansing and prep work of the base metal, in addition to selecting the best filler product, are also advice necessary components of efficient welding techniques. By adhering to these finest techniques, welders can decrease the risk of porosity development and generate top quality, structurally audio welds.

Evaluating and Top Quality Control Measures
Evaluating procedures are vital to find and protect against porosity in welding, making certain the stamina and toughness of the last item. Non-destructive testing techniques such as ultrasonic testing, radiographic testing, and visual inspection are commonly employed to identify possible issues like porosity.
Post-weld evaluations, on important link the various other hand, evaluate the last weld for any flaws, consisting of porosity, and verify that it fulfills specified requirements. Applying an extensive quality control strategy that consists of extensive screening procedures and evaluations is extremely important to decreasing porosity problems and making certain the Click Here overall high quality of bonded joints.
Verdict
In conclusion, porosity in welding can be a typical concern that influences the top quality of welds. By identifying the common root causes of porosity and carrying out ideal practices for prevention, such as appropriate welding methods and screening actions, welders can ensure top quality and reputable welds. It is vital to focus on avoidance methods to reduce the incident of porosity and keep the honesty of bonded structures.
Comments on “What is Porosity in Welding: Common Sources and Reliable Remedies”